2. Efficient Transportation
Bag-in-box products are more convenient to ship and transport. Their rectangular-shaped package takes up less space and are able to easily be stacked together. A skid comprises 50 bag-in-box units but only 36 plastic pail units. This means
more bag-in-box products can be shipped at once. As a result, CO2 emissions are lowered because fewer trucks are needed to transport bag-in-box products.
Similarly, for inbound freight, there can be 3,000 empty bags-in-boxes per skid and only 132 empty pails per skid. Empty bag-in-box packaging can be delivered flat and take up very little space. Using the same logic as above, this means there
are fewer CO2 emissions due to needing fewer trucks to transport empty bag-in-box packages.
Another important note is the ability of bag-in-box packaging to protect the product as it is shipped, so it arrives undamaged and sealed. Compared to pails, the risk of damaged goods is lower for bag-in-box products. With pails, the rigid
plastic can crack and bust, especially when the product is stacked too high and/or when a truck hits a bump on the road. This can also happen when pails lean forward if the driver needs to brake hard or if the bales are facing inward.
Bag-in-box is more flexible due to the cardboard and plastic bag, which makes it harder for the packaging to break and product to leak during transportation. Further protection is provided by shrink wrap.
3. Storage Benefits
Once the product arrives at a warehouse or facility, it needs to be stored in the appropriate location to await shipment or for later use. This can be a challenge due to small and tight spaces. Bag-in-box’s simple shape and size help
minimize space requirements. When stacked, there is no dead space between the boxes. On the other hand, pails are usually circular. When stacked, there is a dead space because they do not fit evenly next to each other, as shown below.
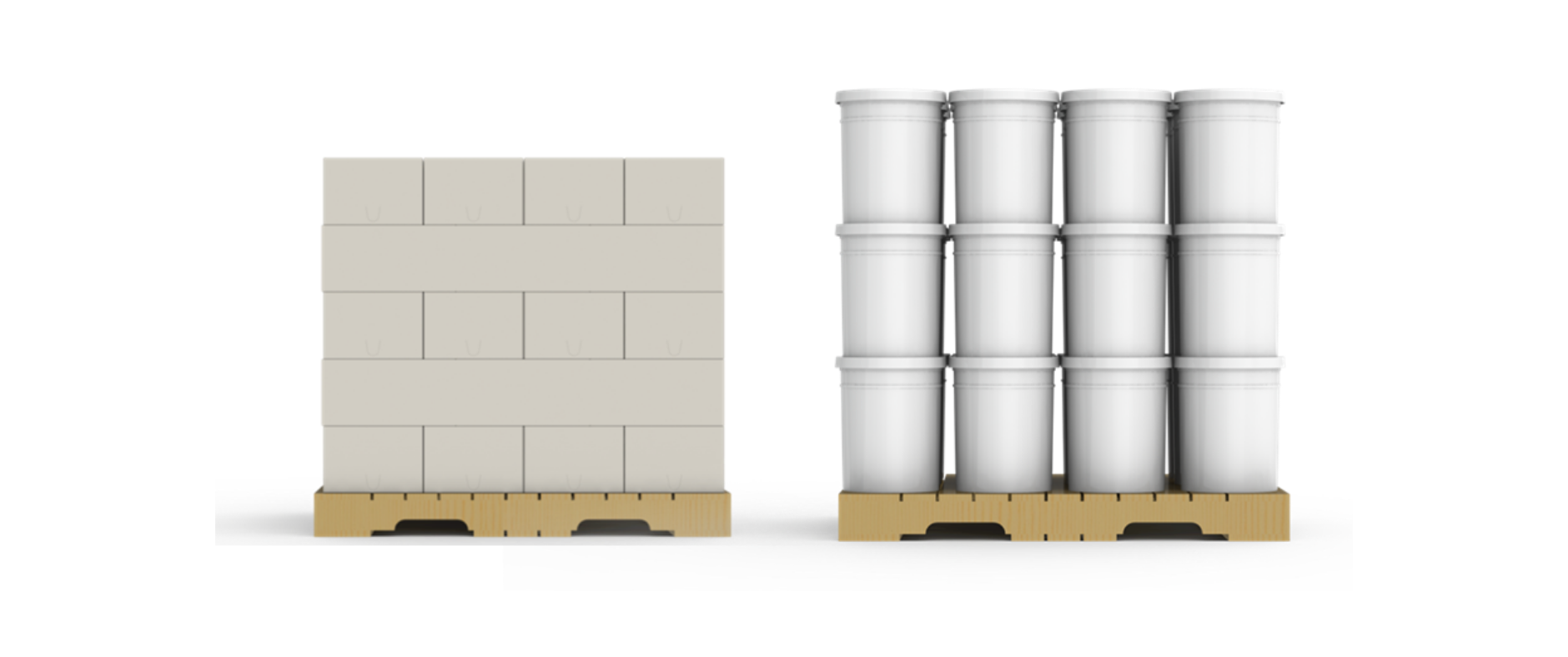
In total, there is a 39% reduction in cubic feet for bag-in-box compared to pails. Bag-in-box skids, for example, are 33 cubic feet for 200 gallons. Pail skids are 59 cubic feet for 180 gallons. That’s 20 more gallons of product
in 26 less cubic feet for bag-in-box.
4. Ease of Use
Beyond just efficient transportation and storage, the rectangular shape of bag-in-box makes it easier for employees to carry or haul the products to wherever they are needed. Once there, to help with dispensing, there are conveniently
placed spigots that release product when opened and block product when closed. This means product can be dispensed without the bag-in-box ever leaving the storage shelf or other flat surface. This is more convenient for customers because,
unlike a pail, it does not require additional labor and strength to lift and pour product out.
Other common issues with plastic pails include heavy surging or glugging when product is poured out, as well as extra time and effort to scrape the sides to use all available product. With the bag-in-box spigot, customers can dispense
a specific amount of product, eliminating overflow and extra mess. The spigot feature also allows a 99% evacuation rate, meaning nearly all the product inside the bag can be used without hassle, so customers receive the full value
of what was purchased more easily.
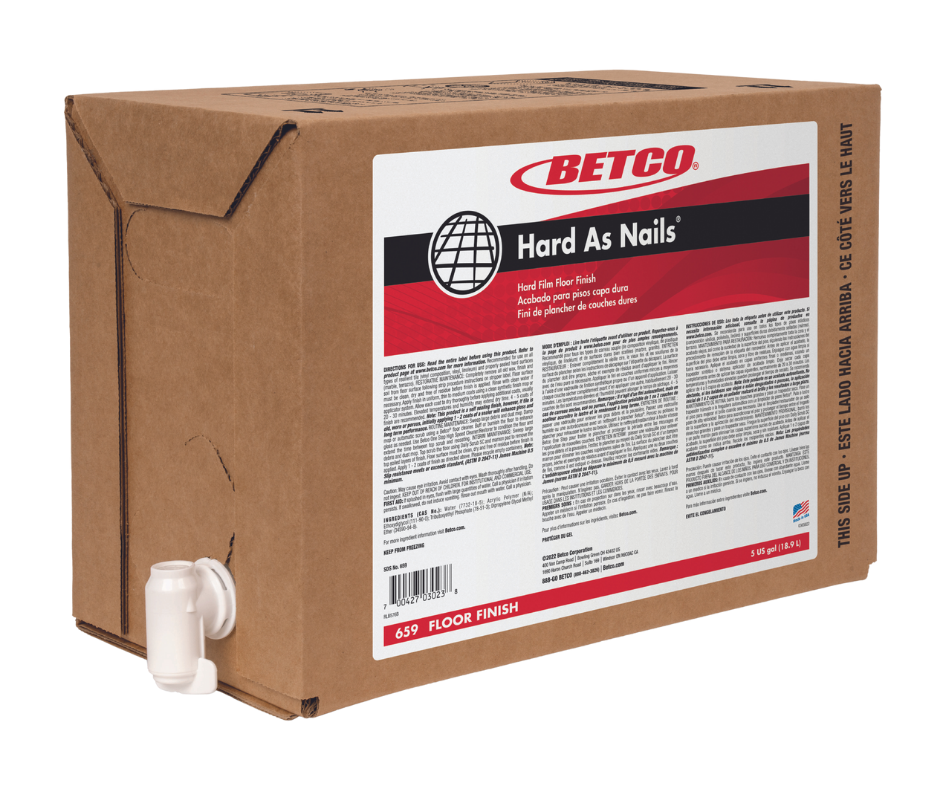
Betco Bag-in-Box
Betco has made the switch to the bag-in-box packaging to improve sustainable efforts and help eliminate our carbon footprint. We believe this change helps our customers and the environment simultaneously through many benefits, including
manufacturing, transportation, storage, and application.
For more information, click here. If you have any questions about bag-in-box, please fill out our online contact us form, or call
1-888-GO-BETCO to speak with a representative today.